Why and how I developed a 10 times better toothbrush (as an ex-F1-engineer)
Why and how I developed a 10 times better toothbrush (as an ex-F1-engineer)
Where I came from - F1 work
I grew up in the engineering companies of my grandfather and father, who specialized in exhaust-system emission- and noise-reduction technologies since the 1960s. When I started to study mechanical engineering at ETH Zuerich in the 80s I was among the first students ever to be educated in CAD (Computer Aided Design. Teached by a Professor from Dornier aircraft, working on clumsy IBM/Catia workstations). Of course I immediately tried to apply the new technology in my father’s exhaust-system company, where prototypes were designed, assembled and optimized largely by hand in days and weeks, for the large manufacturers like VW, and many racing teams, like McLaren, BMW, AMG.
But those CAD systems were extremely expensive and one couldn’t really design and optimize pipes and exhaust systems with them yet. I started to study computer science at University of Zuerich and when working in the Computer Graphics lab of Prof. Stucki there, I came in contact with Silicon Graphics Workstations and Software. So I developed Virtual Reality CAD-software (in C++, running on Silicon Graphics workstations. In the 80s! With Silicon Graphics toolkits. SGI was a milestone.), that allowed exhaust- and pipe-designers to develop complex systems within minutes and optimize them in a way it had never been possible before. Here is a video showing the "Virtual Reality CAD software" I had developed in the 1980s/90s:
In my 20s I studied mechanical engineering, computer science and economics, and developed software and sold it at the same time. My professor wanted me to write a dissertation, but that was totally uninteresting for me, I was doing so much exciting and lucrative work already...
I further optimized and sold the software packages worldwide for the next 20 years until most F1-teams (among many others, Schumacher and Senna were powered by my designs and I even met them) and many auto-manufacturers (BMW, Mercedes, VW, Ford, Ferrari, Porsche…) had been a customer (and until all the big CAD-System manufacturers had copied us).
McLaren was the first F1-customer, when Senna was their driver. I was invited into the Senna-box in Hockenheim, to watch and study exhaust-system handling during testing. When I was there he had a famous clash with M. Schumacher during training.
Here you see my first complete exhaust-manifold-design delivered to a F1-team. During the work on it I tested and optimized the software I had developed.
What I did up to this point had a lot to do with mass-tailoring, applying rapid-prototyping technologies and programming.
Working on new ideas
When the market seemed more and more saturated after about 20 years, I started working on new ideas where I could apply my knowledge. One was "tailored sun-clips for eyeglasses". I had a very expensive pair of designer eyeglasses, and I thought about how I could make them tinted in an elegant and low-cost way. The solution I developed was thin tinted films clipped to the correction eyeglasses from the inside, tailored based on the eyeglass shapes customers faxed to us (by just putting the eyeglasses on a fax-machine). The eyeglasses just looked tinted after clipping them in, and one could hardly see the clips.
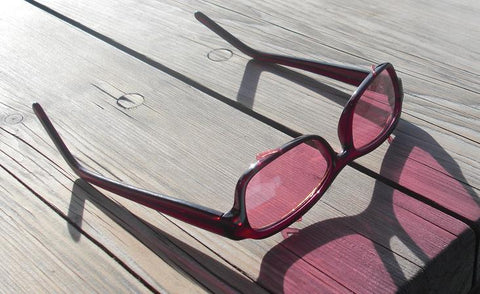
The software was developed by a mathematician for us, "contour detection", pre AI. The tailoring work was fully automatic, and the films were simply just completely laser-cut. The idea was "mass-tailoring". In the end I gave that up, because we charged 29.- US$, and that was pretty much how much it cost us, on average, to acquire a new customer through Google ads (which we knew a year later). (Nowadays, I probably wouldn't give up so easily. Just trying to increase prices a bit, optimize the conversion rate, and it might be a good business). The eyeglass manufacturers soon after started to sell an additional pair of correction glasses, tinted, at very low prices (as low as 99.- back then).
Taking a time out for thinking what to do next
I took a time out, and spent a winter in Morocco, to think about what I could do next, where ideally I could deliver the most benefit for society, based on my knowledge and experience thus far.
When walking through the old town of Marrakech, I saw a “dentist’s practice”, where all that was done was pulling teeth. Even young women sat in the waiting rooms, waiting to get relieved from their tooth-ache by pulling a tooth….It made me aware that tooth-cleaning is still a very big problem. And not just in "poor" countries.
All of my life I had experienced myself how bad oral hygiene led to myriads of tooth problems and high costs for repairs. I used to think that was normal. The time-out let me think about the problem fundamentally and extensively researching the internet and patent databases. I had a lot of experience with CAD-design, programming, and designing complex mechanical parts, and rapid-prototyping technologies like 3D-printing. I thought if someone had the arsenal of tools necessary to solve the denture-cleaning-problem, then it was me. There hadn't been any meaningful innovation in the toothbrush business for decades (electric ones were developed in the 1950s. And in the scientific literature I read that they offer just a 5% better cleaning performance "under lab conditions". I tested them and was very disappointed. In real life they were not better than my manual toothbrush and a dentist friend confirmed it to me).
The main problem of hand-toothbrushes is that users have to position them manually everywhere they want to clean, and in the right angles, and with correct pressures, and for a substantial amount of time.
Thus the hand of the user determines 99% of the cleaning success, independent of the kind of manual/electric toothbrush used.
Therefore I thought about a “mouthpiece”-toothbrush, that was individually tailored, then 3D-printed, based on scans of the teeth. I thought I was the only person on earth thinking about such a crazy device, but in the patent databases I saw that dentists had thought about something like this for decades already, but without an idea how such a thing could be made a reality, because they didn’t have the CAD- and manufacturing-possibilities or -knowledge. But that confirmed that my idea wasn't so stupid after all.
Here you see one of the numerous mouthpiece patent applications made by dentists over the last decades: "Kelly" 1980 (there are even decades earlier similar applications):
All these patent applications were for "one-size-fits-all"-trays. I knew that in this form this could never clean well because dentures were far too different and the materials shown could never ever adapt well enough. Also it was impossible to bristle these devices with the conventional toothbrush bristles shown. Consequently all these designs never became real products.
The first mouthpiece-toothbrush - going viral in 2012
Back home I discussed the idea with dentists and dental hygienists, and then designed a first prototype and an animation (using Blender) showing how the brush worked.
Here you see a screenshot from design-work - the bristles positioned automatically on the tooth surfaces by the software I developed:
The website was blizzident.com. I uploaded the video to youtube, put up a little website and sent emails to 5 blogs who I thought could be interested. 2 weeks later 3 blogs published something, which was picked up by more and more media and even made it into TV. Here is the youtube-video that went viral and had over 1 M viewers within 3 weeks in 2013:
We received thousands of emails, and orders and calls from VCs like Tim Draper (early Tesla and Space-X investor) and big toothbrush manufacturers (e.g. the head of Philips Sonicare) who were interested to invest. We had designed, manufactured and marketed the first working mouthpiece toothbrush and thus introduced a completely new category of toothbrushes.
An image from the 1st patent application.
Foto of the very first 3D-printed tailored mouthpiece toothbrush. From a first production run with about 30 individually designed brushes. Those first brushes were still relatively big but very nicely usable. But there was even an Internet-meme then made by a Japanese customer who showed using it, exaggerating how "difficult it was" to take it into the mouth. Only because he didn't bother to RTFM ;-)
Blizzident 3.0 - everything further optimized. This was a model that allowed flossing at the same time!....The grip was a case for a floss roll....And there was a tongue-cleaner too.
A major design-challenge was how to mount traditional toothbrush-bristles in the 3D-printed plastic bodies. In the toothbrush-factories this is fully automated - machines are anchoring the bristles in holes in the handles by pushing them in together with tiny metal blades, which are pressed into, thus are firmly mounted, in the plastic body. (This makes all toothbrushes recycling nightmares). There was no way to do this automated “anchoring” with our 3D-printed bodies, and also I wanted to avoid the metal blades at all cost, because of the environmental impact.
The software first calculated the placements of the bristles on the denture, then created the "housing" with "U-channels" holding the bristles (optimising wall-thicknesses and final bristle-placements along the way).
The bristles were mounted in the plastic bodies in "U-channels". Thanks to 3D-printing we could also create special tools allowing to mount the bristles in the bodies (by hand!).
This is what a calculated final 3D-printed plastic body looked like. It was also optimised to use only an absolute minimum amount of the expensive bio-compatible 3D-printing material.
The harsh reality of manufacturing and delivering a working product
Taking this from animation and first prototype to real mass-tailoring and manufacturing was far more difficult and time-consuming than I had anticipated (despite my nearly 3 decades of experience in these fields). Over the following years we developed and then further refined mass-tailoring software, that in the end (in 2019) designed the tailored mouthpiece-toothbrush completely automatically, based on denture-scans the customer sent us.
Denture scans we tailored to
The product design went through two major updates every year for seven years. Every time I had ideas for clear improvements (in cleaning efficacy, ease of use, manufacturing cost), we built prototypes, tested them, developed software extensions, and introduced the new product.
Here you see the latest "Blizzident Brush 4.0" in 2019. We had developed "bristle-strips", nylon-fibers melted together by laying a hot wire onto them for a few seconds. Then these were mounted in slits in the 3D-printed toothbrush-body. (First dry, later with liquid silicone). Like this we had much denser bristle-fields, and the assembly time was much quicker. The plastic mouthpiece was even optimized for printing completely without supports, for cost reasons.
During the whole development time we also always wrote patent applications before releasing anything publicly. This is very time-intensive and expensive too.
It was extremely demanding work over the many years, non-stop thinking and working, and we spent much more money than we ever earned every year. I was convinced that somewhen in the future it would be standard for “everyone” to get an own tailored toothbrush, and we would build a big mass-tailoring business similar to Invisalign.
Mass-tailoring and mass-manufacturing of 3D-printed toothbrushes. Every brush you see here, was different, individually tailored...
But the costs for the customers were prohibitive. Getting tooth-scans or -impressions was a huge cost factor (150-250 US$), and printing toothbrushes with bio-compatible material with resin-based 3D-printers was very expensive too, so that the product would always be a “product for the rich”. Even just the pure printing process was difficult to dial-in, we had to design the parts so they worked for resin-based 3D-printing. We had lots of failed prints, and it was very rarely true mass-tailoring/manufacturing, although it became better over time (and nearly flawless in the end, after 7 years of experience).
Lockdown-shocks, copycats, and drastic change
Then, in early 2020, the covid-lockdown-shock made me pause and re-think everything again. What I did was still, after 7 years, financially not viable, and, beginning in 2017, people tried to copy us with cheap non-tailored mouthpiece toothbrushes, that didn’t even work at all (!), but customers bought them like crazy (!) (Amabrush made millions with these) and forgot about us. Also, I was convinced that the lockdowns would cause enormous economic harm and would make it even more difficult to survive with such an expensive "luxury" product. (The cost of the first tailored brush was always between 200-300 US$ and replacement brushes 50$, while one brush could be used for about 3 months.
When one works so extensively and for such a long time on a specific product category, one gains a lot of experience and knowledge in that field. That gives the foundation and self-confidence to think completely outside the box to solve a problem. I have thought about solving the tooth-cleaning problem many years more than most dentists I assume. Over the years I had developed the idea that other materials / configurations than the traditional toothbrush bristles could be much better suited for tooth-cleaning. I always thought about maybe “knitting” a mouthpiece-“scrubbing-brush” out of the nylon-fiber-filaments used in toothbrushes. Because that could be manufactured at low cost and would provide the dense field of bristles needed, and could nicely adapt to the different denture shapes.
Finally the sponge idea
Then one evening, when doing the dishes by hand with a kitchen-sponge, I marveled about how well these super simple cleaning-tools adapt to surfaces and cavities. I had used cleaning-sponges so many times in all these years, without ever thinking about the similarity to “surface- and cavity-cleaning” in dentures…. suddenly the light-bulb went on…. Open-cell silicone sponges (not the typical kitchen-sponges) basically consist of the same kinds of fibers that are used in toothbrushes and are perfectly hygienic because they are anti-microbial and easily washable... A "one-size-fits-all" sponge adapts perfectly to all denture-shapes and the forces are wonderfully evenly distributed.
Here you see the very first prototype of a mouthpiece sponge-toothbrush developed in early 2020. I still thought in terms of a "device/handle that is holding a sponge". Albeit the yellow part was cut from soft EVA-foam, it was much too harsh in the mouth, and washing/drying after toothbrushing was a problem:
The first released (and thought-to-be final) version was then finally simply a mouth shaped silicone-sponge with a biting slit in the top and bottom surface:
The silicone-fibers would glide over tooth surfaces and cavities cleaningly while biting and grinding in the biting-slits. That was super-simple, elegant and “genius”, it worked really well, but still not good enough, as we soon detected. The fibers didn’t intrude into the interdental regions well enough.
But I still didn’t think enough out-of-the-box, which cost me an additional two years of development time. I thought now, we still needed conventional toothbrush-bristles for the interdental cavities. I still didn’t know (or still didn’t think hard enough) that this could be totally avoided in the first place.
At first still a too complicated sponge-design (in hindsight)
Our toothbrush-bristle-strips could ideally be used for this now (but who knows, maybe I would have been forced to find the perfect solution we have today immediately, if these bristlestrips hadn't been available). But now we had to develop methods to mount them firmly in the sponges. Which still occupied us in the following two years and which made the brushes still expensive to manufacture. And not as comfortable to use as we liked them to be.
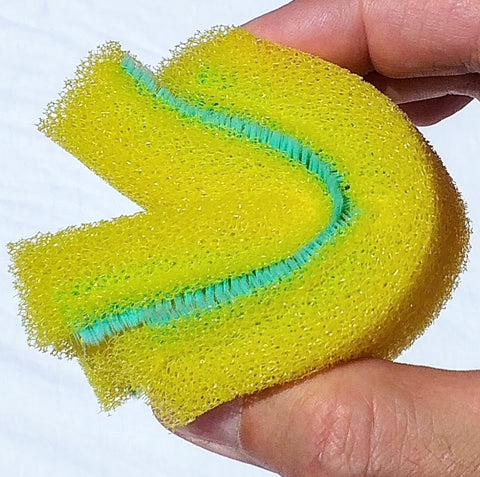
In the first year we purchased sewing machines and developed methods and tools to sew the bristle strips into the sponges. Because of the sewing process the sponges had to be straight, and the user had then to bend them into U-shape before inserting them into the mouth. The sponges worked very nicely (as dentist Dr. Tristan Peh from Singapore showed in a fantastic, hilarious video, where he didn't even use it correctly and still achieved a fantastic cleaning result :-) :
But of course I was still thinking about much better ease-of-use.
Why hadn't I immediately thought about "glueing" our bristle-strips into the sponges with liquid silicone, like we had done with the later 3D-printed brushes? Maybe because it sounded ridiculous at first, to "glue" something into a sponge… I had this idea a year later and it worked fantastically. Like this we could return to the mouth-shaped sponges, and that made usage much easier again. But still not "super-easy", and still pretty expensive to manufacture, because of the manual labor involved.
"Blizzbrush 5.0"
Another year later: finally the perfect sponge design
A sponge that can be taken into the mouth must be as soft and light and small as possible, to avoid any type of gag-reflex. And ideally the sponge would just consist of sponge material and nothing else, to make it as soft as possible. Two years after beginning the sponge work I finally had the idea to simply cut many small sponge-ribs into the walls of the biting-slits, perpendicular to the tooth-surfaces, which can then wonderfully intrude into the interdental cavities and swipe them cleaningly.
Blizzbrush 6.0 - we still had to optimize it further with broader slits over the molars
The sponge-ribs intrude into the interdental regions and cavities super-nicely.
This makes the sponges super-easy to use (even by the elderly, and by children), and much less expensive to manufacture, because manufacturing can be fully automatic. Soon we will be able to manufacture at costs similar to simple manual toothbrushes now.
Blizzbrush 7
Our brushes even made it into the Colgate "toothbrush museum" in the meantime
In the meantime we learned that our toothbrushes are even in the Colgate "toothbrush museum" and the head of Colgate toothbrush design said while showing one of our brushes: "mouthpiece toothbrushes are the future". Here is the video Colgate posted on their Linkedin page recently:
But with the "toothcleaning-sponge" we are even many years ahead of what the world considers to be "mouthpiece toothbrushes" today. There is no "mouthpiece" with a handle anymore, just cleaning bristles.
The "toothcleaning-sponge" works perfectly now, and is super-easy to use
Customers, Dentists and Registered Dental Hygienists confirm that our brushes are working perfectly and a European University is starting a large clinical study now, where they want to test whether the Blizzbrushes can even be used in carehomes.
Problem solved.
(Why "10 times better"? Cleaning time is about 15 seconds, 12 times faster than the 3 minutes necessary with manual non-electric brushes. And all teeth are cleaned at the same time, the user doesn't have to think about where to position the brush manually anymore. How many times better is that? 5 times better? 12×5 is even 60 times better…).
Regrets and conclusions
The main regret is, why didn't I have the sponge idea immediately, 10 years earlier? In my case, only the years long development time led me to this "crazy" idea, to the ideal solution. I think it's often like this, good thinking costs much time. And if this solution had been so easy and obvious, then a few other of the 8 billion fellow humans on this planet would have had this idea much earlier than me.
An important conclusion for me is, it is often much better to think about possible solutions much more intensively and much longer than I often did. The work ethos I grew up with, never to sit around "idle" for more than a few minutes each day, led me to often jumping right into working hard to solve a problem as quickly as possible (quickly resulting in months- and years-long work). Maybe it would have been better to take many more months initially just thinking and researching, to maybe find the sponge idea right away? But I also had to earn money, meaning to be able to offer a working product as quickly as possible. And in hindsight everything always seems to be much more obvious than it actually was back then.
Chris Martin,
Nov 10th 2023
Blizzbrush prices currently are 7.99 in a 12-pack (costing 95.88), 9.99 in a 6-pack (costing 59.94),
or 12.99 in a Trial-3-Pack costing 38.97 here: